
Carbon Dioxide (CO2) in air is normally measured in Parts Per Million (ppm). At 1,000 ppm CO2, one million air molecules would contain a mixture of 999,000 air molecules and 1,000 CO2 molecules. The most common CO2 sensors are known by the engineering term Non-Dispersive InfaRed, or NDIR. An NDIR CO2 sensor shines infrared light through a gas sample in a sample chamber (see Figure 1). Sensitive photo-detectors measure the intensity of the infrared light after it passes through the gas sample.

CO2 molecules are opaque to 4.26 micron infrared light while the rest of the air molecules are not. So the intensity of the infrared light is diminished proportionally to the number of CO2 molecules that are present. Measuring the resultant light intensity measures the number of CO2 molecules present.
Sensor Drift
The most common light source for NDIR sensors is an incandescent light bulb. In these bulbs, an electric current passes through a metal filament and heats it until it starts to glow. The glowing filament is extremely hot and some of the metal atoms boil off the filament and fly around inside the bulb. Most of these atoms re-adhere to the filament when the power is turned off, but some move far enough away from the filament that they condense onto the glass envelope. Over time, this thin metal coating slightly reduces the amount of light emitted by the bulb. This reduction is perceived by the sensor as an increase in CO2 concentration. Also, when the metal atoms condense back onto the filament, they can slowly shift the spectrum of the emitted light which can affect the perceived infrared light intensity and CO2 concentration.
Automatic Background Calibration
One way to compensate for sensor drift is through automatic background calibration. Outdoor levels of CO2 are generally around 400 ppm. Since people are the main source of CO2 inside a building, when a building is unoccupied for 4 to 8 hours the CO2 levels tend to drop to the outside level. Automatic background calibration uses the sensor’s on-board microprocessor to remember the lowest CO2 concentration that occurs every 24 hours. The sensor assumes this low point is the outside CO2 level.
The sensor is also smart enough to discount periodic elevated readings that occur if a space is occupied for 24 hours a day over a few days. Once the sensor has collected 14 days worth of low CO2 concentration periods, it performs a statistical analysis to see if there has been any small changes in the background levels readings that could be attributable to sensor drift. If the analysis concludes there is drift, a small correction factor is made to the sensor calibration to adjust for this change. This automatic calibration requires that at least three of the last 14 days have space CO2 levels that reach 400 ppm for an hour or more.
The Combined Effect of Temperature and Barometric Pressure on CO2 Measurement
Another way to compensate for sensor drift is through a dual channel design. In this setup, one photo detector and filter is used for CO2 measurement and works the same as in a single channel design. The second photo detector and filter is a reference and uses a wavelength that is not affected by air molecules. About once a day, the sensor takes a reading using the reference channel. Any change in this reference measurement indicates a change in the optics of the sensor which can lead to drift. The sensor then automatically corrects the CO2 measurement from the first channel to prevent the drift.
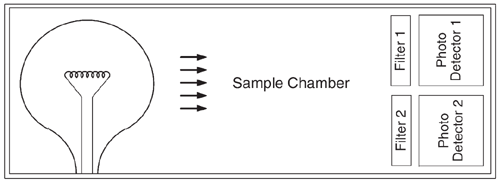
While the reference channel corrects for changes over time, a field calibration using nitrogen gas will immediately restore the highest level of accuracy.
If you have additional questions, please call your BAPI representative.